Vidura
posted this
10 October 2024
Some general considerations about practical design, geometry and switching parameters:
If we consider the conventional motors like brushed DC motors, universal motors, AC induction motors and also different types of synchronous motors with or without PM we find that they are all powered continuously during the rotation. But we find a completely different situation when dealing with pulsed motors. Here only in limited sectors during the revolution power is applied to the coils. But on what does it actually depend in what moment the pulse has to be applied and for how much degrees of the rotation? To understand how to approach the ideal parameters for the switching lets examinate some drawings from Robert Adams and from his assistant engineer John Martin. We will see at the first glance that the aspect ratio of the magnets are drawn very different:
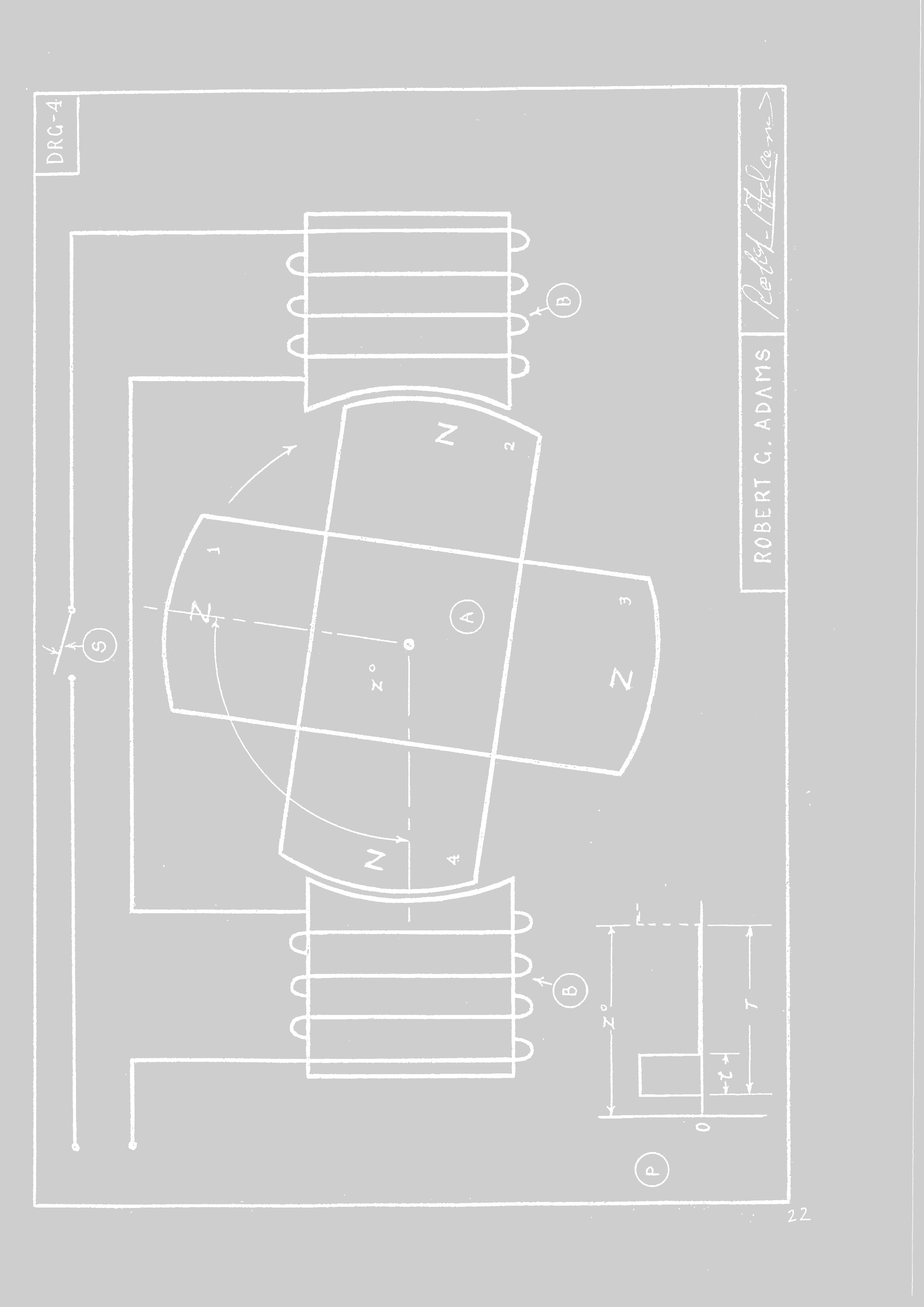
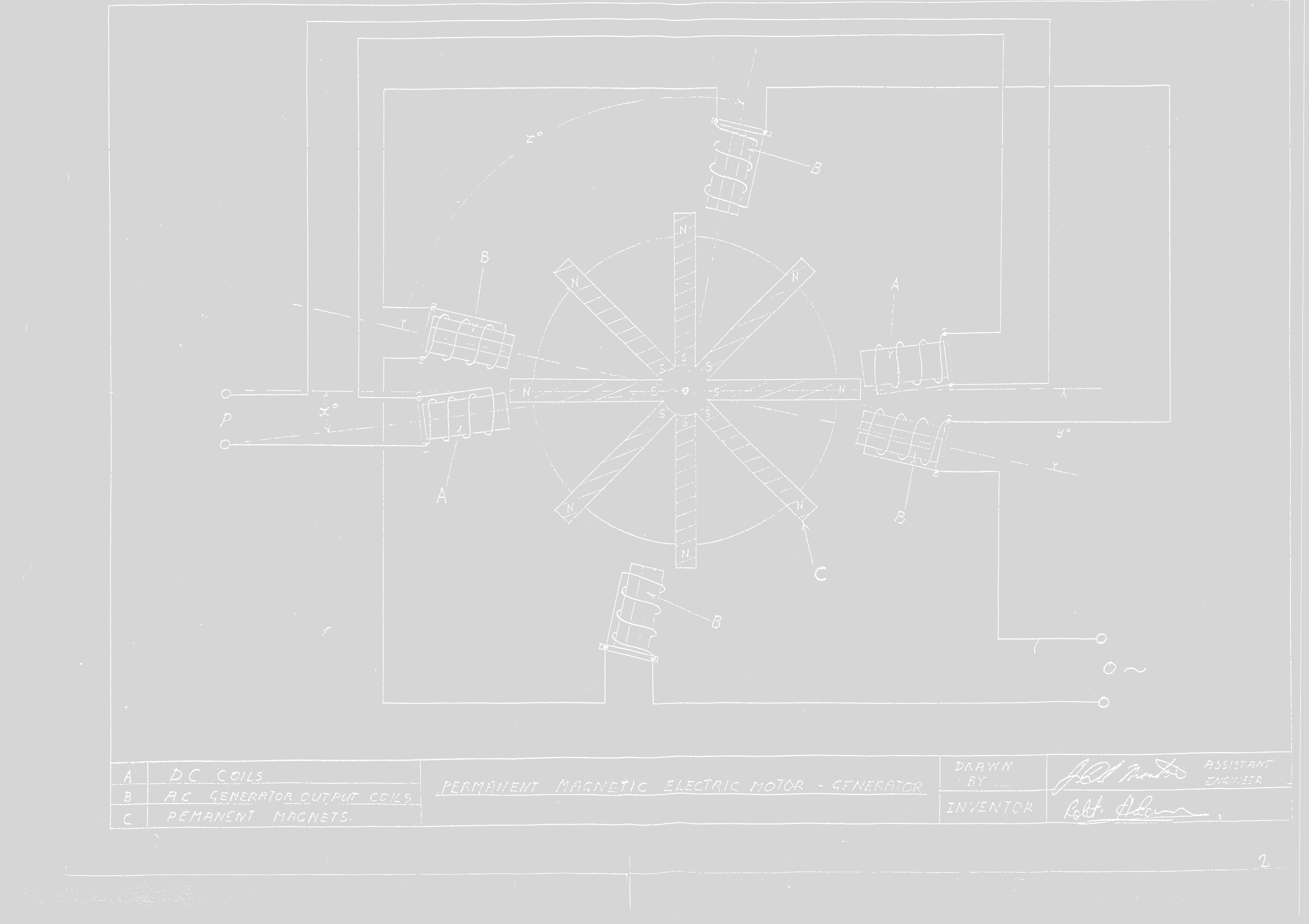
Mr Adams has drawn broad magnets and drive cores in his sheets. Electric engineers know the importance of the cross-sectional area for a powerful magnetic force.
In contrast the drawings made by John Martin seems to be more conceptual to show different types of configurations and connections.
We can examine different conventional machines, motors and generators both, and see clearly that the area of the magnetic components is directly related to the power ratings. This does not mean that only broad and wide magnetic components will give a significant performance, but the total of the cross-sectional area will be always proportional to the maximal power rating. But of course, also many small coils and magnets will add up to make a powerful motor or generator. In this drawing by the way we can see that short disc-shaped ferrite magnets are used:
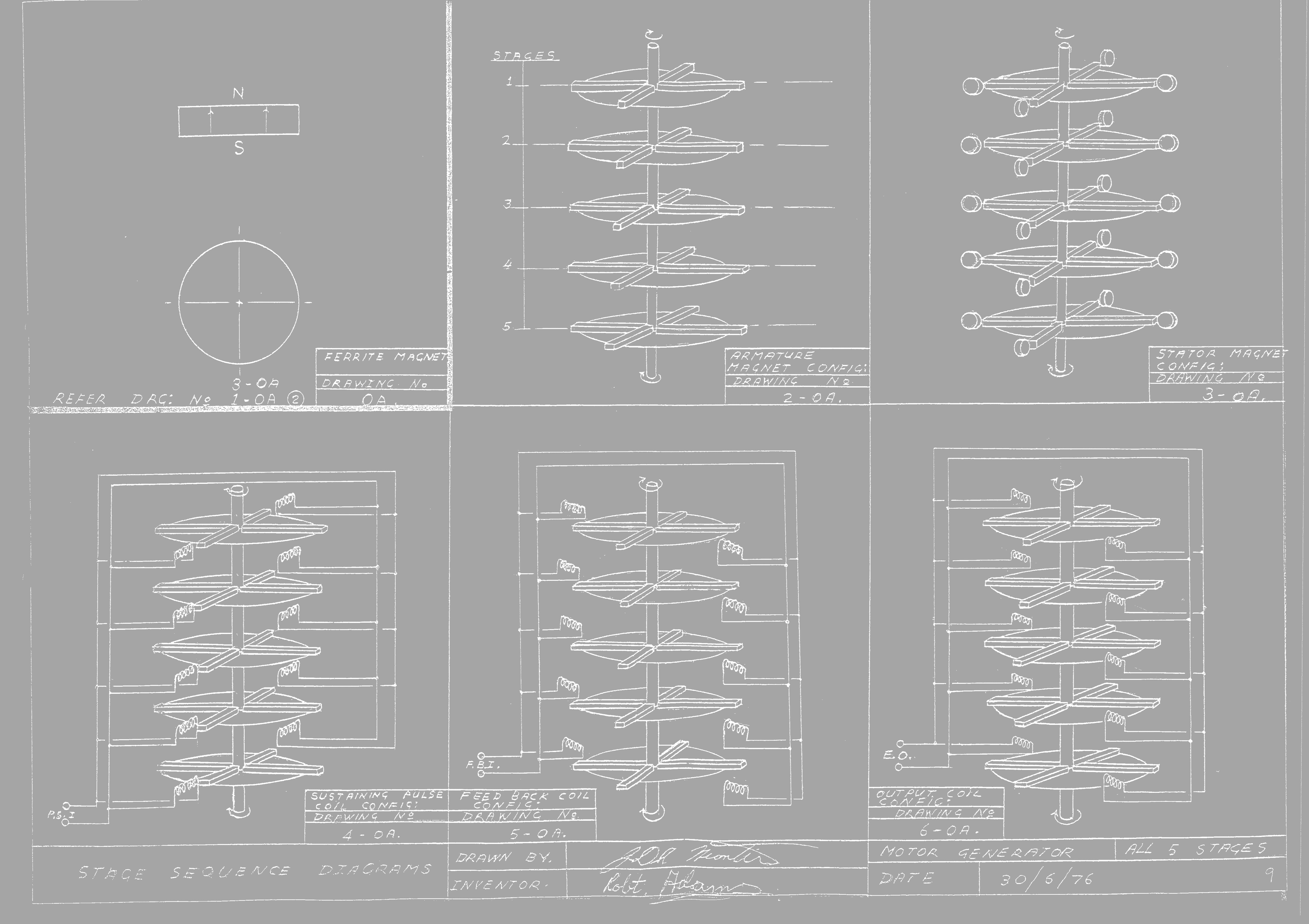
It becomes clear that Robert Adams has designed a wide variety of different machines with different shapes of magnets and coils. So, we cannot expect a recipe or design rule which applies to all of them.
Coming back to the switching parameters, it is also clear that these have to be chosen according to the geometric layout of the motor. As I have shown in the YT video of the magnetic force between rotor and stator, there is a very defined position of the magnet, when the attraction becomes strongest. In this position the drive coil has to be magnetized at its maximum. But how many degrees of the rotation this position occupies, depends on the size and shape of magnets and cores. The same is true for the angle where the effective work of the motor is performed.
For example, in the drawings below:
In the position of the first drawing the attractive force is still small, the pulse is initialized. The exact position varies depending on the inductance of the coil and the delay of magnetization of the core material.
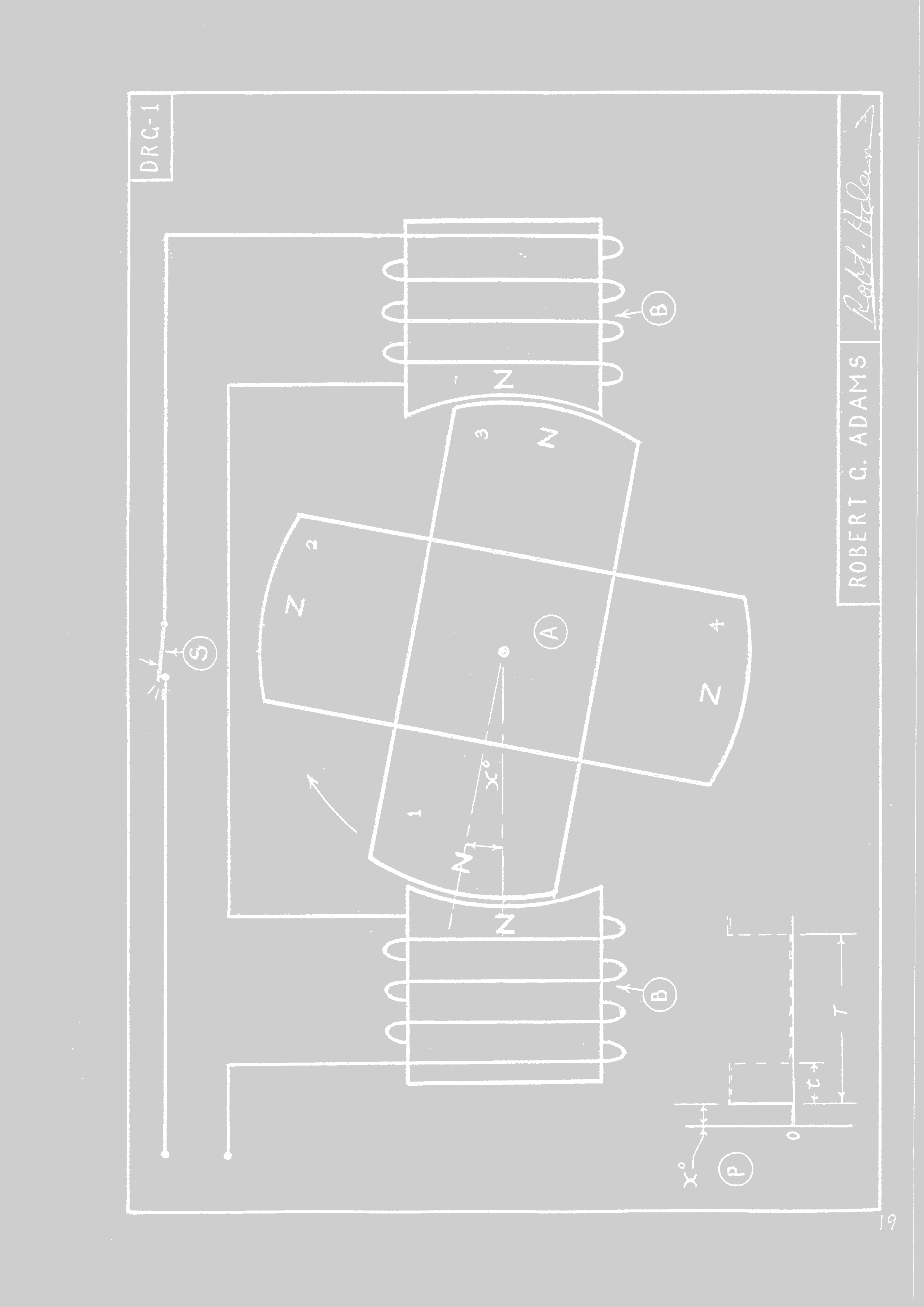
In the next drawing the relative position of the rotor is near the maximum of the magnetic attraction force and the pulse is turned off. Again, there is some delay in the demagnetization of the core material, which still is repelling the overlapped magnet.
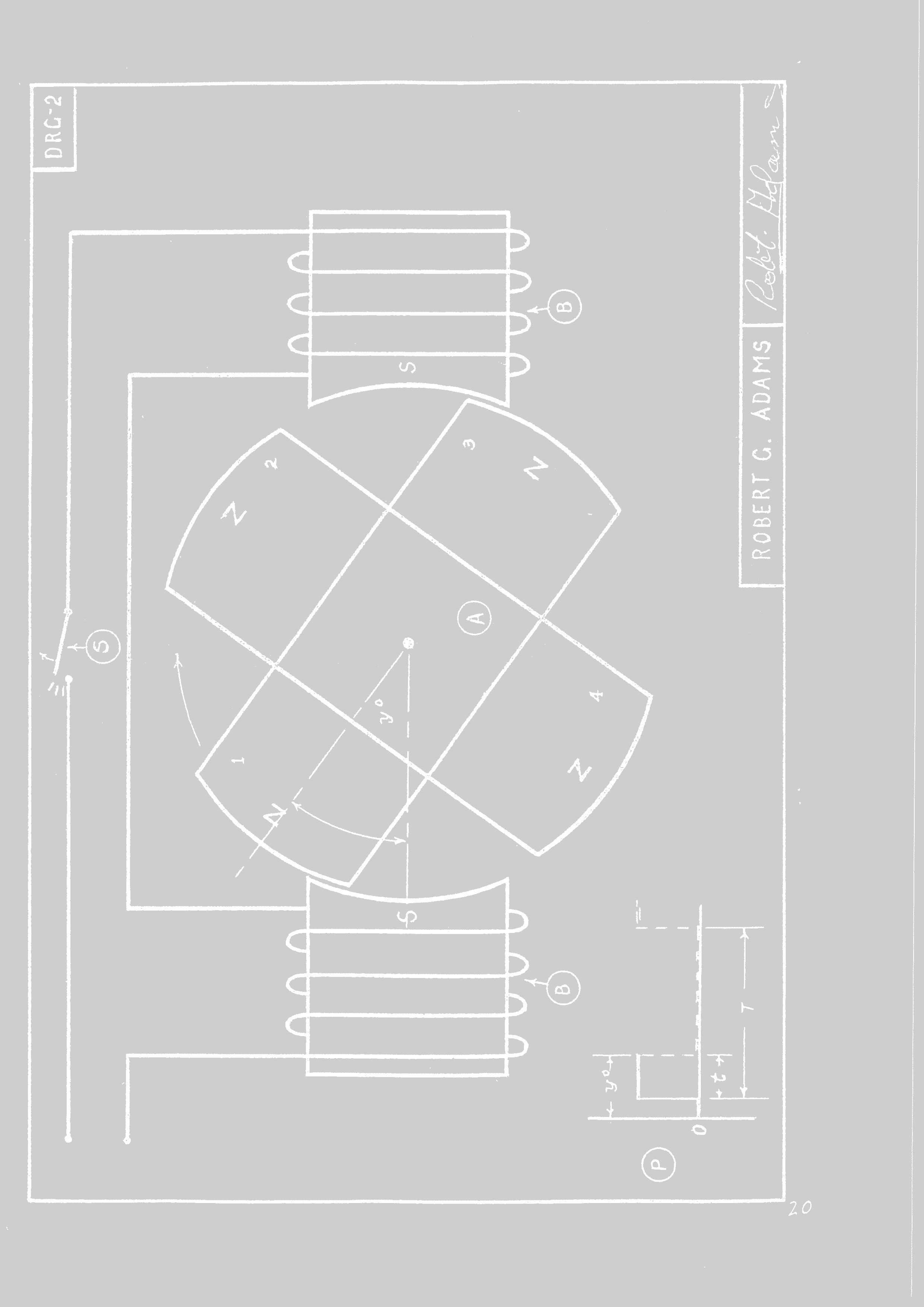
When the rotor moves a bit further, the cores demagnetized completely, and the next approaching magnet will attract the core from the other side, here the second part of the work period starts. This part is for free, as no electrical energy needs to be applied.
Therefore, a motor of such a geometric shape similar as in this drawing would perform work almost continuously during the whole rotation, but would require a pulse of less than 50% DTC to drive it at full power. And with appropriate switching techniques around 80% of the input power could be recovered for recycling. I think these are excellent conditions for an OU machine.